Roller Service and Repair | Improve Efficiency & Save Costs
- Ben Perren
- 11 hours ago
- 5 min read
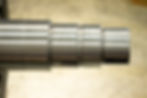
Rollers are a critical component across a wide range of industries, from printing and packaging to manufacturing and industrial production. Yet, despite their essential role, rollers are often overlooked when it comes to preventive maintenance and timely repair. Regular roller service and repair are not just about avoiding downtime—they are strategic investments that enhance operational efficiency, reduce long-term costs, and preserve equipment longevity.
At RollerTec Inc., we specialize in an array of professional roller service and repair solutions designed to keep your operations running at peak performance.
Introduction to Rollers
Industrial rollers are essential components in modern manufacturing, playing a crucial role in various industries such as manufacturing, processing, and production. These rollers are used in conjunction with high-speed sorting equipment to handle materials and move products efficiently. With the ability to operate at high temperatures and withstand heavy weights, industrial rollers are a vital part of many industrial applications. At the heart of these rollers are expertly designed and fabricated cores, which can be made from a range of materials including steel, aluminum, and urethane. Regular maintenance, including roller repair and recovering, is crucial to prevent costly repairs and extend the lifespan of these critical components.
Types of Rollers
There are various types of rollers, each designed to suit specific industrial applications. These include chrome rollers, rubber rollers, and urethane rollers, among others. Each type of roller has its unique characteristics, advantages, and disadvantages. For instance, chrome rollers are known for their high durability and resistance to corrosion, while rubber rollers offer excellent grip and traction. Urethane rollers, on the other hand, provide a cost-effective solution for applications where high abrasion resistance is required. Understanding the different types of rollers and their applications is essential for industries that rely heavily on these components. By selecting the right type of roller for a specific application, industries can minimize downtime, reduce replacement costs, and optimize their processes.
Why Regular Roller Service Matters
Routine roller maintenance is vital for maintaining the precision and performance of your equipment. Over time, rollers are subjected to wear and tear caused by friction, pressure, environmental factors, and other elements such as heat and chemicals. Without proactive servicing, minor surface imperfections or internal damages can escalate into major failures, leading to production delays and costly replacements.
Key benefits of regular roller service include:
Enhanced operational efficiency
Reduced risk of unexpected breakdowns
Extended lifespan of rollers and associated machinery
Improved product quality and consistency
Lower total cost of ownership
By scheduling regular inspections and service intervals, companies can avoid emergency repairs and ensure continuous production output.
Cost-Saving Advantages of Timely Roller Repairs
Deferred maintenance often results in compounded damage, requiring complete roller replacement rather than simple repair. In contrast, early-stage repairs—such as resurfacing, regrinding, or core balancing—can restore roller performance at a fraction of the replacement cost.
Choosing professional roller repair services also provides:
Lower replacement frequency: Extend the usable life of your rollers.
Minimized production downtime: Quick turnaround times to get you back online.
Energy efficiency gains: Well-maintained rollers reduce machine strain and energy use.
Predictable maintenance budgets: Eliminate surprise costs associated with urgent replacements.
At RollerTec Inc., our goal is to help clients save money while ensuring their equipment delivers optimal results year-round. We are capable of handling a wide range of repairs, showcasing our proficiency in advanced techniques and technologies.
Common Roller Service Solutions
Our roller service and repair offerings are tailored to meet the specific needs of each operation. Services typically include:
Resurfacing and Regrinding: Restoring the roller’s surface to original specifications to ensure proper material transfer and minimize wear.
Bearing and Core Repair: Addressing internal issues to maintain alignment, load distribution, and structural integrity.
Cover Replacement and Recoating: Applying new covers or coatings suited to the application environment—whether for high-friction, chemical resistance, or temperature resilience. We use specialized roll covering compounds to formulate these covers for specific service conditions, enhancing the quality and durability of the rollers.
Balancing and Alignment: Precision balancing to reduce vibration, enhance speed capability, and protect adjacent machinery.
Inspection and Diagnostics: Comprehensive evaluations to detect early signs of wear or mechanical stress.
We leverage advanced technologies and industry-best practices to ensure that every repaired roller meets or exceeds performance expectations.
Reverse Engineering Capabilities
Reverse engineering is a critical capability in the field of industrial rollers, allowing companies to create new matching rollers for existing applications. This process involves carefully inspecting and measuring the existing roller, and then using this information to design and fabricate a new roller that meets the exact same specifications. Reverse engineering is particularly useful when the original manufacturer is no longer in business or when the original specifications are no longer available. By using reverse engineering capabilities, companies can extend the life of their equipment, reduce replacement costs, and minimize downtime. This expertise is also essential for designing and fabricating multi-component rollers, which require precise tolerances and specifications to perform optimally.
Fabrication and Manufacturing
Fabrication and manufacturing are critical processes in the production of industrial rollers. These processes involve designing and building the roller core, selecting the appropriate materials, and applying the desired coating or covering. The fabrication process requires specialized equipment and expertise, including machining, grinding, and balancing. By using state-of-the-art technologies and techniques, companies can produce high-quality rollers that meet exacting specifications and perform optimally in their intended applications. The use of advanced materials, such as silicone and ceramic, can also enhance the performance and durability of industrial rollers. Whether it’s creating a new roller from scratch or refurbishing an existing one, the fabrication and manufacturing process is essential for producing rollers that meet the needs of modern industry.
Common Causes of Failure
Industrial rollers can fail due to a variety of reasons, including wear and tear, corrosion, and improper maintenance. One of the most common causes of failure is worn or damaged bearings, which can cause the roller to vibrate or seize. Another common cause of failure is a damaged or corroded core, which can weaken the roller and cause it to fail prematurely. Improper maintenance, including infrequent inspection and repair, can also contribute to roller failure. By understanding the common causes of failure, industries can take proactive steps to prevent downtime and reduce replacement costs. Regular inspection, maintenance, and repair, including journal repair and recovering, can help extend the life of industrial rollers and optimize their performance. Additionally, the use of cost-effective solutions, such as regrinding and resurfacing, can help minimize downtime and reduce costs.
How Roller Service Impacts Operational Efficiency
Downtime and inconsistent product output can be direct results of worn or improperly functioning rollers. Regular service ensures that rollers maintain:
Proper grip and traction on production materials
Consistent surface pressure and material transfer
Minimal vibration and machine wear
Stable, high-speed operation without risk of slippage or jams
Necessary functionality to meet operational needs
Facilities that invest in proactive roller maintenance often report measurable improvements in overall equipment effectiveness (OEE) and product throughput.
Why Choose RollerTec Inc. for Roller Service and Repair?
With decades of experience supporting printing, packaging, and industrial production sectors, RollerTec Inc. offers:
Industry-leading expertise in all roller types and applications
Customized service programs based on client needs and operational demands
High-quality materials and precision workmanship
Rapid turnaround times to minimize downtime
Comprehensive service documentation for your maintenance records
A specialized team dedicated to delivering high-quality roller solutions, ensuring expert repairs and tailored solutions to meet specific needs
Our commitment to quality and customer satisfaction has made us a trusted partner for companies seeking reliable roller solutions.
Schedule Your Roller Service Consultation Today
Do not wait for minor roller issues to escalate into major operational disruptions. Investing in regular roller service and repair is a smart, cost-effective strategy for maximizing your production capabilities.
Contact RollerTec Inc. today to schedule a service consultation or learn more about how our customized roller solutions can help your business stay efficient, productive, and profitable.